Material Compatibility
Published date: 07 Aug 2023
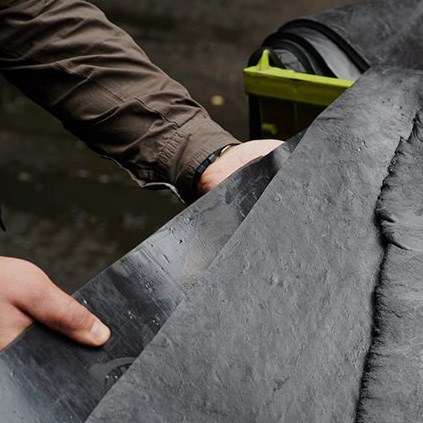
In today’s article, let’s take a deep dive into some of our more popular materials – silicone, fluorocarbon (FKM), and EMI/RFI rubber – highlighting their applications, characteristics, advantages, and limitations.
One of our most popular and common materials, silicone is a versatile elastomer known for its excellent temperature resistance, flexibility and hygienic properties.
It has a continuous working temperature range of -60 to 230 degrees, making it the material of choice for manufacturers of aerospace and outer-space craft manufacturers. Additionally, Silicone offers great resistance to weathering and UV exposure, making it suitable for exposure in outdoor applications. Even under sustained pressure, silicone is able to maintain its sealing properties. This, coupled with its flexibility with variations in temperature, make silicone a great all-rounder for aerospace and healthcare applications.
With sustainability currently a key focus for both SBR’s core industries and the organisation, SBR also produce from recycled silicone grades, utilising waste, used part and excess silicone materials from different products and industries to re-produce and form new parts for various end applications and industries including; civil engineering, aerospace and MoD. Click here to learn more…
There are, however, some limitations to the use of silicone in some industries. For example, silicone has a poor tear and abrasion resistance, meaning that it’s performance in dynamic applications is limited. It’s tensile strength is also limited, at around 10kPa, which means that for high-force and high-pressure applications silicone may not be the correct material for you. You can find further information here.
Viton, DuPont’s trademark name for FKM or Fluorocarbon, offers benefits over silicone that might make it, in some cases, superior. In general, the chemical structure of FKM makes it an ideal material for applications that require strong chemical compatibility with hydrocarbons, oils and fuels. Additionally, it’s tensile strength is greater than that of silicone – around 14kPa – with a higher rating of abrasion- and tear-resistance, which allows it to perform well in more demanding, high-pressure applications. Depending on the application, FKM can offer superior durability that would prevent the need for unnecessary downtime due to product failure. Additional information and characteristics can be found here.
Southbourne Rubber has, for many years, supplied silicone gaskets, pads and custom solutions that resist electromagnetic and radio frequency interference. These EMI/RFI resistant silicone products are filled with electrically-conductive materials, often copper, metal, graphite, nickel or silver, reducing the impact of electronic interference from electronics or electromechanical devices. These products have been utilised more and more in aviation and military applications, and are installed in vulnerable areas where existing electronic components could be affected by other electromagnetic emissions. If you are looking to seal components that are susceptible to electronic interference, normal silicone and FKM may not be the correct choice for you. For additional information on EMI/RFI, click here.
To summarise, each material featured has specific properties that benefit different applications
Silicone
A good all-rounder in terms of sealing, as well as standard levels of tensile strength that would be most suited to lower pressure and impact applications.FKM
Best suited for applications that require higher levels of durability than silicone, as well asa higher chemical resistance to hydrocarbons.
EMI/RFI Silicone
Provides specific protection for those critical applications that require the utmost in termsof safety and resistance to electronic interference.